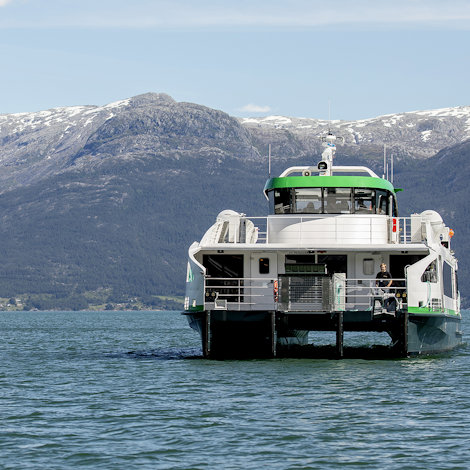
We can add value to your heat sink solutions by enhancing thermal performance in both small and large heat sinks. We know from experience that the improved thermal performance you gain in your heat sinks by using aluminium extrusions often leads to less weight, higher efficiency, and a lower total cost.
The math is simple: In the design phase, cost reductions of more than 50% can be achieved. In the purchasing phase, only margins can be reduced.
Beside the need for cooling, you have the opportunity to integrate other functionalities when you use aluminium extrusions. These include:
We can also optimize air-cooled heat sinks through simulation, such as the optimization of aluminium profiles.
It all starts with an idea. It makes good sense for you to utilize our material specialists and engineering experts during an early stage of your design and development needs. With their competence, they can in addition to design advice, also give alternatives for alloys and surface treatment.
We offer heat sink solutions in aluminium for liquid or air cooling. Whichever solution you prefer, there are many factors to consider, such as the choice for heat conduction.
The flow of liquid or air is what conducts, or “carries away,” the heat from your heat source. The trick is to get the flow to work hand in hand with the solid heat sink. This can be done by using a circular hole or rectangular channel throughout your liquid heat sinks or by identifying the optimal fin design for your air-cooled heat sink.
A high fin ratio is often required to manage high-powered heat sinks. However, weight savings can be a challenge in such scenarios, due to the delicate balance between airflow and fin design. For standard heat sink fin heights, there could be more weight-saving potential by designing the fin as conical vs. straight.
With liquid cooling, circular or rectangular design could create additional value for your product.
Choosing fin design inside the hole increases surface area. An increase of surface area often results in lower temperature gradients. But because these channel designs cannot be machined, an aluminium extrusion is the best solution. Rectangular-shaped channels increase the cooling effect even more due to the larger contact area closer to the heat source.